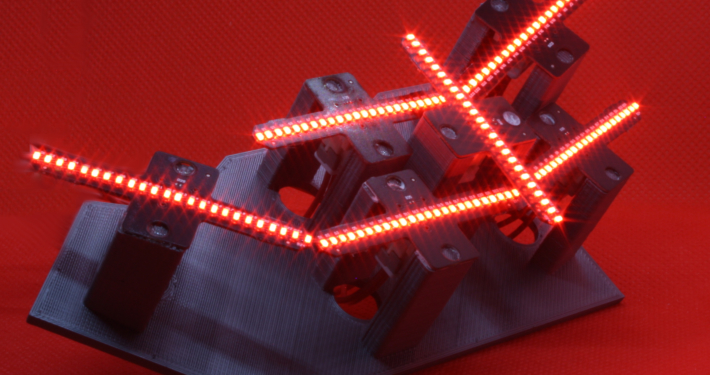
It burns at vosla. Gas flames shoot horizontally at glassy pistons, which will shortly afterwards carry an ice layer. Wherever the extremes collide, where fire and ice prevail, there is glass in play. And for an eternity.
Everywhere this precision. As with the helix production, as in the construction of the lamp frame with the narrowest tolerances. Every lamp has over 20 heats of fires in the form of highly accurate measurements before it is put into circulation – in the supreme discipline – of automotive lighting.
The glass is no different. It’s much more alive than metal, it’s not that easy to tame. For example, quartz glass is so tough that it can withstand even extreme temperature fluctuations without further treatment in the processing chain itself.
For tempered glass that looks different. This is where a complicated, sensitive process comes into play, where a lot of know-how and experience is required – hard glass technology – the core competence of vosla.
Nevertheless, more than a tenth of a millimeter deviation from the nominal value is not tolerated here at vosla even in glass processing.
For over 70 years vosla has been processing glass here. Soft glasses for long – lasting signal lamps, quartz glass for the demanding lamp types of airfield lighting in the runways of airports worldwide.
Hard glasses for extremely versatile automotive and non-car applications, halogen lamps that have to withstand ten times the internal pressure of a car tire are the core business of vosla. 30 bars prevail inside a glass bulb of about 1.5 cubic centimeters when the halogen lamp is in operation.
A tempered glass must be tempered if you expect it such loads. Annealing refers to the defined cooling phase of hard glasses in a given time unit. For this purpose, it is exposed to a strict temperature regime, the so-called tempering curve, which according to the requirements puts it in an ideal state of tension.
Only then is the glass able to withstand the further processing stages, which are icy than ice. Hard glass blocks are cooled in the moment of filling with halogen gas, in the liquid nitrogen bath shock-like down to about -200 ° C, while through the thin exhaust tube, the filling gas is drawn into the flask. The glass is sealed. This creates the characteristic nipple on the piston tip, the so-called pump tip.

Sometimes it gets colorful
But often the glass does not stay alone. Sometimes color comes to it. In close cooperation with companies specializing in glass coatings, very special products are created for the tuning and design market in the aftermarket segment. They can be yellow, blue or shimmering in rainbow colors – as in the latest product, the HIR2H, a toughened glass lamp with an infrared coating.
As one of the last processing steps is often still, depending on the application, the dome of the glass bulb dipped in color. This only happens with automotive lamps. Some are blue, gray, other dome colors even shimmer metallic.
Earlier, decades ago, when lamps were still simple light bulbs, the number of manual operations still predominated in manufacturing, in which even the glass dome was still used by hand and then fused. Today, this happens in the midst of a very complex and tightly meshed process, where timing must be as precise as annealing.
All this – especially because of the glass – is today a well-tempered alternating bath of the elements of fire and ice.